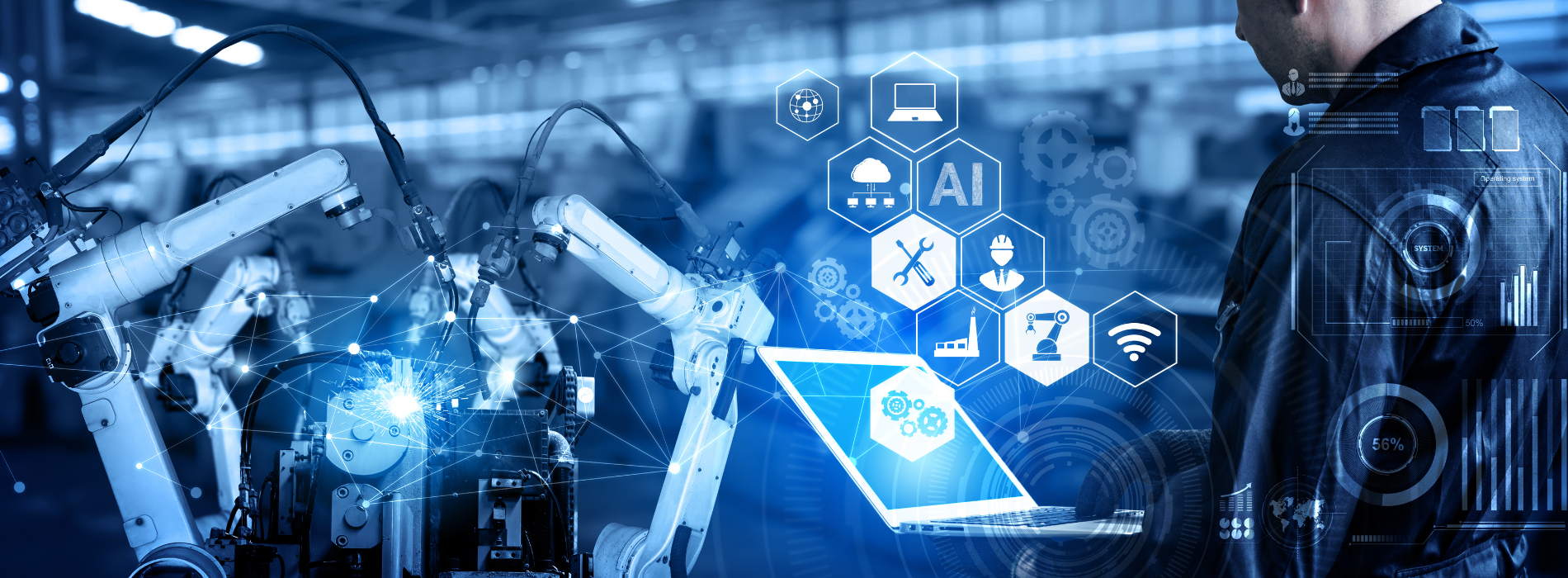
ARTIFICIAL INTELLIGENCE & ROBOTS - October 2023
Robots at the Workplace: Considerations from a Workplace Safety Perspective
By Gary Low, Alex Goh and Tan Jia Yi (Drew & Napier LLC)
I. Introduction
Singapore’s resident total fertility rate decreased to an all-time low of 1.04 in 2022,[1] continuing a downward trend over the years. Coupled with a tight employment market, Singapore companies may make increasing use of technology in the workplace to augment and support their human workforce amidst manpower constraints. Robotics is a “significant” growth area for Singapore and the Singapore government sees “many industry sectors increasingly adopting robotics solutions to enhance productivity, safety and quality”.[2]
II. Trends and observations about robots in the office workspace
Whilst industrial robot deployment in factory spaces has been prevalent for several decades, we see robot deployment increasingly extending to other workplace settings such as white-collar office settings.
For instance, in South Korea, robots are now scurrying around the office “completing mundane tasks like fetching coffee, delivering meals and handing off packages …, cruis[ing] around on their own, moving from floor to floor on robot-only elevators and sometimes next to humans, rolling through security gates and entering meeting rooms.”[3] These abilities reportedly helped an employee to save time and “focus on her work, eliminating the distraction of walking to a coffee shop”.[4] In 2017, the Straits Times ran a feature on a humanoid robot NAO which could take on various receptionist tasks. This included providing “a range of information from the phone numbers of recommended accounting firms to details about nearby restaurants including cuisine type and pricing”. [5] The NAO robot, which was reported to be able to communicate in English and Japanese, could also “occasionally break into a dance too”.[6] As the COVID-19 pandemic turbocharged the virtual meeting market, telepresence robots have also gained more popularity in recent years by helping to provide better virtual meeting experiences. Professional cleaning robots may also become more common in office workspaces.
III. Workplace safety risks and regulations
When deploying robots in the workplace, safety should be a foremost consideration to employers. In a case heard by the Canadian courts[7], a workplace incident involving a human worker and a robot rendered the human worker a paraplegic. In that case, a robot pressed against the worker’s back when he was carrying out what he thought was a ”quick fix” to fix the tooling and the overheating electrode associated with a robotic cell,[8] and the employer was subsequently convicted for three offences under Canada’s Occupational Health and Safety Act.[9] While this case occurred in a manufacturing facility, it is not inconceivable that there could be accidents from robot deployment in other workplace settings (e.g. an office robot crashing into a human worker or spilling hot coffee which it was delivering to a human worker).
Under Singapore law, employers have a statutory duty to take, so far as is reasonably practicable, such measures as are necessary, to ensure the safety and health of its employees at work.[10] Such measures include but are not limited to ensuring that adequate safety measures are taken in respect of any machinery, equipment, plant, article or process used by those persons.[11] In the event of any contravention of this duty, the employer shall be guilty of an offence,[12] and the court in such scenario has the power to mete out various penalties including a fine and/or imprisonment.[13] If the contravention continues after conviction of the first offence, the employer shall be guilty of a further offence and shall be liable to further punishments.[14]
It is also the specific duty of an occupier of a workplace to take all reasonably practical steps to ensure that any self-acting machines in the workplace poses no risk to the safety and health of any persons working in the workplace.[15]
Bodily injury to human workers resulting from the use of robots may also expose employers to a negligence lawsuit given their common law duty to take reasonable care for their employees’ safety.[16] Should an employer be found to be in breach of its duty of care, the court may grant damages as compensation to the employee to put him/her in the same position as he/she would have been if he/she had not sustained the injury.[17] Apart from such financial liability, such incidents may further cause reputational damage for employers.
IV. A framework for safe robot deployment in the workplace
How should an employer consider safety issues arising from robot deployment in the workplace? Conducting a proper risk assessment, implementing risk elimination/control measures and reviewing/revising risk assessments are essential elements of a proper workplace safety framework in this regard.
In Singapore, the Workplace Safety and Health (Risk Management) Regulations[18] mandate, amongst other things, that:
- employers are to conduct a risk assessment in relation to the safety and health risks posed to any person who may be affected by his/her undertaking in the workplace;[19]
- employers are to take all reasonably practicable steps to eliminate any foreseeable risk to any person who may be affected by his/her undertaking in the workplace;[20]
- where it is not reasonably practicable to eliminate the abovementioned risk, the employer shall implement such reasonably practicable measures to minimise the risks and such safe work procedures to control the risk[21] - this may include substitution, engineering control, administrative control, and provision and use of suitable personal protective equipment;[22] and
- employers are to maintain records of risk assessments and any measure or safe work procedure implemented;[23] and
- employers are to review and, if necessary, revise the risk assessment at least once every three years - a review and revision of a risk assessment is mandatory upon the occurrence of any bodily injury to any person as a result of exposure to a hazard in the workplace or where there is a significant change in work practices or procedures.[24]
Risk assessments
In conducting risk assessments for deployment of robotic systems, the Workplace Safety and Health Guidelines on Safe Use of Machinery[25] (the “WSH Guidelines”) may provide a good starting point.
The WSH Guidelines state that before conducting a risk assessment, adequate preparation must be done, including (1) the formation of a risk assessment team consisting of personnel in charge of various aspects of the work activity, and (2) the collation of relevant information such as the machine operating manual provided by the manufacturer or supplier and information on the limits of the machine.[26]
The WSH Guidelines also explain the three key steps of a risk assessment, namely, (i) hazard identification (ii) risk evaluation and (iii) risk control.[27] Briefly:
- hazard identification involves identifying hazards associated with each work activity and considering the personal health risk factors of employees involved;[28]
- risk evaluation involves assessing the potential severity of the machine hazard, determining the likelihood of the incident or ill-health that could occur while working with the machine, and estimating the risk level of the work activity based its severity and likelihood;[29] and
- risk control means selecting measures to reduce the potential risk to an acceptable level.[30]
The fact that a manufacturer has already performed a risk assessment for achieving safety in the design of the robot does not exempt an employer from carrying out its own risk assessment for workplace safety and health risks arising from the deployment of the robot.
Hazards arising from robot deployment may include, amongst other things, collisions, crushing, jamming, repetitive impacts and risks of musculoskeletal disorders on the part of human co-workers,[31] as well as battery hazards.[32]
The risk profile may differ depending on the type of robot being deployed. For instance, the risk profile presented by “caged industrial robots which should not share their workspace with anyone except on rare occasions” [33] may be very different from collaborative robots “which can share theirs with a limited number of operators”.[34] With the advent of mobile robots which can travel around a “quasi unlimited workspace”,[35] risks are “multiplied by the presence of the other workers” who “are not operating the robot while still sharing the same environment”.[36]
Implementation of risk elimination/control measures
Employers are required to take all reasonably practical steps to eliminate any foreseeable safety and health risks in the workplace[37] – it is only where it is not reasonably practicable to eliminate such risks that employers shall implement such reasonably practicable measures to minimise the risks and such safe work procedures to control the risk.[38]
It could be difficult in some cases to eliminate all risks arising from robot deployment as this may involve the modification of the design of the machine to eliminate the risk inherently.[39] Manufacturers and suppliers may be unwilling to modify the design and features of the robot to suit the requests of individual users.
In such scenarios, employers will need to be conscientious in implementing risk control measures and safe work procedures. These may include substitution, engineering control, administrative control and the provision and use of suitable personal protective equipment in compliance with the Workplace Safety and Health (Risk Management) Regulations.[40]
Employers must also specify the roles and responsibilities of persons involved in the implementation of risk control measures and safe work procedures.[41]
Reviewing and revising risk assessments
Employers should ensure that they review their risk assessments for deployment of robotic systems at least once every three years. This is to ensure that any unintended gaps/blind spots in the previous risk assessment are identified and rectified, and to prevent complacency.
Where there is a change of work practices or procedures, or where there is an accident in the workplace due to robot deployment, employers should immediately conduct a review and revision of the original risk assessment.
V. Conclusion
As employers tap on robots in the workspace, they should be prudent to implement measures for the safety and health of their human employees. This would assume an even greater importance in the days ahead as robot-human interactions in the workplace are expected to intensify.
AUTHOR INFORMATION
Gary Low is a Director of the Dispute Resolution Practice and Co-Head of the Criminal Law Practice at Drew & Napier LLC.
Email: gary.low@drewnapier.com
Alex Goh is a Director of the Dispute Resolution Practice at Drew & Napier LLC.
Email: alex.goh@drewnapier.com
Tan Jia Yi is an Associate of the Dispute Resolution Practice at Drew & Napier LLC.
Email: jiayi.tan@drewnapier.com
REFERENCES
[1] Department of Statistics Singapore, ‘Births and Fertility’ <https://www.singstat.gov.sg/find-data/search-by-theme/population/births-and-fertility>.
[2] Ministry of Trade and Industry Singapore, ‘Speech by 2M Tan See Leng at the National Robotics Programme 6th Anniversary Event and Launch of the Aerial Arena’ <https://www.mti.gov.sg/Newsroom/Speeches/2023/02/Speech-by-2M-Tan-See-Leng-at-the-National-Robotics-Programme-6th-Anniversary-Event>.
[3] John Yoon and Daisuke Wakabayashi, ‘Meet Your New Corporate Office Mate: A ‘Brainless’ Robot’, The New York Times <https://www.nytimes.com/2022/11/17/business/south-korea-office-robots-naver.html>.
[4] Ibid.
[5] Samantha Boh, ‘Humanoid robot NAO takes on receptionist tasks at rental office firm Crosscoop Singapore’, The Straits Times <https://www.straitstimes.com/singapore/humanoid-robot-nao-takes-on-receptionist-tasks-at-rental-office-firm-crosscoop-singapore>.
[6] Ibid.
[7] R v Matcor Automative Inc., [2017] O.J. No. 4257.
[8] Ibid.
[9] R.S.O. 1990, c. O.1
[10] Workplace Safety and Health Act 2006 (2020 Rev Ed Sing), s 12(1).
[11] Workplace Safety and Health Act 2006 (2020 Rev Ed Sing), s 12(3)(b).
[12] Workplace Safety and Health Act 2006 (2020 Rev Ed Sing), s 20.
[13] Workplace Safety and Health Act 2006 (2020 Rev Ed Sing), s 50(a) and s 50(b). In the case of a natural person, the Court may impose fine not exceeding S$200,000 or imprisonment not exceeding 2 years or both. In the case of a body corporate, the Court may impose a fine not exceeding S$500,000.
[14] Workplace Safety and Health Act 2006 (2020 Rev Ed Sing), s 50(c) and s 50(d).
[15] Workplace Safety and Health Act (General Provisions) Regulations (Cap 354A, Reg 1, 2007 Rev Ed Sing), reg 18. It is to be noted that in the previous iteration of Regulation 18, this specific duty was confined to factories. However, by way of Workplace Safety and Health (General Provisions) (Amendment) Regulations 2011 (S 517/2011 Sing), the word “factory” was deleted and substituted with the word “workplace”, which would extend to offices.
[16] Chandran a/l Subbiah v Dockers Marine Pte Ltd [2010] 1 SLR 786 at [19].
[17] Gary Chan Kok Yew, The Law of Torts in Singapore (Academy Publishing, 2nd Ed, 2016) at [20.036].
[18] Workplace Safety and Health (Risk Management) Regulations (Cap 354A, Reg 8, 2007 Rev Ed Sing).
[19] Workplace Safety and Health (Risk Management) Regulations (Cap 354A, Reg 8, 2007 Rev Ed Sing), reg 3(1).
[20] Workplace Safety and Health (Risk Management) Regulations (Cap 354A, Reg 8, 2007 Rev Ed Sing), reg 4(1).
[21] Workplace Safety and Health (Risk Management) Regulations (Cap 354A, Reg 8, 2007 Rev Ed Sing), reg 4(2).
[22] Workplace Safety and Health (Risk Management) Regulations (Cap 354A, Reg 8, 2007 Rev Ed Sing), reg 4(3).
[23] Workplace Safety and Health (Risk Management) Regulations (Cap 354A, Reg 8, 2007 Rev Ed Sing), reg 5.
[24] Workplace Safety and Health (Risk Management) Regulations (Cap 354A, Reg 8, 2007 Rev Ed Sing), reg 7.
[25] Workplace Safety and Health Council and Ministry of Manpower, ‘Workplace Safety and Health Guidelines Safe Use of Machinery’ < https://www.tal.sg/wshc/-/media/tal/wshc/resources/publications/wsh-guidelines/files/wsh_guidelines_on_safe_use_of_machinery.ashx>
[26] Ibid at 6.
[27] Ibid at 8.
[28] Ibid.
[29] Ibid.
[30] Ibid at 9.
[31] Bruno Belzile and David St-Onge, ‘Safety First: On the Safe Deployment of Robotic Systems’ <https://link.springer.com/chapter/10.1007/978-981-19-1983-1_14> at 431. The link to the Creative Commons license is http://creativecommons.org/licenses/by-nc-nd/4.0/.
[32] Ibid at 434.
[33] Ibid at 433.
[34] Ibid.
[35] Ibid.
[36] Ibid at 433.
[37] Workplace Safety and Health (Risk Management) Regulations (Cap 354A, Reg 8, 2007 Rev Ed Sing), reg 4(1).
[38]Workplace Safety and Health (Risk Management) Regulations (Cap 354A, Reg 8, 2007 Rev Ed Sing), reg 4(2).
[39] Belzile and St-Onge, above n 32, at 427.
[40] Workplace Safety and Health (Risk Management) Regulations (Cap 354A, Reg 8, 2007 Rev Ed Sing), reg 4(3).
[41] Workplace Safety and Health (Risk Management) Regulations (Cap 354A, Reg 8, 2007 Rev Ed Sing), reg 4(4).